Alumina Bubble Bricks belongs to a kind of ultra-high temperature material energy-saving insulation material. It uses alumina hollow spheres and alumina powder as the main raw materials, combined with other binders, and fired at a high temperature of 1750 degrees. As a refractory manufacturer, why are alumina hollow ball bricks widely used? Why recommend alumina hollow ball bricks to customers? This will start with the performance of Alumina Bubble Bricks.

The Manufacturing Process of Alumina Bubble Bricks
Alumina Bubble Brick is a new type of high-temperature insulation material, which is made by smelting and blowing industrial alumina in an electric furnace. With alumina hollow spheres as the main body, it can be made into products of various shapes, with a higher use temperature of 1800°C. The mechanical strength of the product is high, which is several times that of the general lightweight product, and the bulk density is only one-half of the corundum product. Among them, the alumina powder is produced by using reliable industrial alumina as the raw material, using a new high-temperature inverted flame kiln and a scientific calcination process. Manual selection, clear classification, fewer impurities, high conversion rate, stable shrinkage rate, and good consistency.
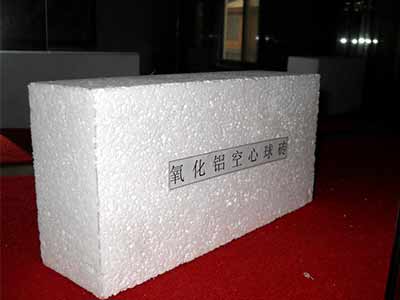
The Performance of Alumina Bubble Bricks
Alumina hollow ball and its products are a kind of light refractory material with excellent high-temperature resistance and energy saving, and it is very stable to use in various atmospheres. Especially it is used in the high-temperature furnace at 1800℃. Hollow balls can be used as high-temperature, ultra-high-temperature insulation fillers, high-temperature refractory concrete lightweight aggregates, high-temperature castables, etc. Hollow ball bricks can be used for high-temperature energy-saving (>30%) inverted flame kilns, shuttle kilns, molybdenum wire furnaces, tungsten rod furnaces, induction furnaces, nitriding furnaces, etc. Obvious effects will be achieved for reducing the weight of the furnace body, transforming the structure, saving materials, and saving energy.
The specific advantages of alumina bubble bricks are as follows.
- The operating temperature is high, up to 1750 degrees. Good thermal stability, the small change rate of the re-burning line, longer use.
- Optimize the structure and reduce the weight of the furnace body. The high-temperature-resistant materials currently used are heavy bricks with a bulk density of 2.6-3.0g/cm. The alumina hollow ball brick is only 1.1~1.5g/cm, the same volume of one cubic meter, the use of alumina hollow ball brick can reduce the weight of 1.1-1.9 tons.
- Save materials. To reach the same operating temperature, the price of heavy bricks is equivalent to that of Alumina Bubble Bricks, and considerable refractory materials are required for insulation. If alumina hollow ball bricks are used, 1.1-1.9 tons of heavy bricks can be saved per cubic meter, and 80% of refractory insulation materials can be saved.
- Save energy. Alumina hollow spheres have obvious thermal insulation properties, low thermal conductivity, and can play a very good thermal insulation effect. Reduce heat dissipation and improve thermal efficiency, thereby saving energy. The energy-saving effect can reach more than 30%.
Obviously, the excellent energy-saving effect of alumina hollow spheres makes it more competitive as a lightweight refractory material. Buyers of kiln lining materials will definitely prefer such superior refractory products. Therefore, not only refractory manufacturers recommend everyone to buy Alumina Bubble Bricks, but also its own advantages that make it so widely used. Alumina Bubble Bricks are widely used, for example, in high temperature and ultra-high temperature furnaces such as petrochemical industrial gasifiers, carbon black industrial reactors, metallurgical industrial induction furnaces. And they have achieved very good energy-saving effects.
For more refractory materials products, please contact us: inquiry@global-refractory.com.