Alumina Silicate Refractory Bricks, for those who do not understand the refractory industry, maybe this is a kind of refractory bricks containing aluminum and silicon. But for people in the refractory industry, there is no such name, only aluminum-silicon-based refractory bricks. So, what are Alumina Silicate Refractory Bricks? What is Alumina-Silicate Refractory Brick? First of all, let’s take a look at the definition, what does aluminum-silicon refractory brick mean?

Alumina Silicate Refractory Bricks, also known as aluminum-silicon refractory bricks, are refractory products containing Al2O3 and SiO2 and are a series of aluminum-silicon refractory bricks. Aluminum-silicon-based refractory bricks have a wide range of applications and occupy a very important position in the refractory application industry. Its usage accounts for more than 40% of the entire refractory products.
By definition, Alumina Silicate Refractory Bricks are a series that includes multiple types of refractory bricks. Below we categorize them to give you a deeper understanding.
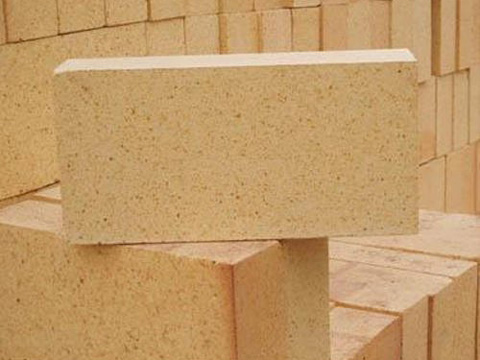
Aluminum-silicon-based refractory bricks are classified in the order of increasing composition from SiO2 content to Al2O3 content.
- (1) Silica brick: SiO2 content ≥93%;
- (2) Semi-silica brick: Al2O3 content is 15%-30%;
- (3) Clay brick: Al2O3 content is 30%-48%;
- (4) High alumina brick: Al2O3 content ≥48%;
- (5) Mullite brick: Al2O3 content ≥72%, SiO2 content ≥28%;
- (6) Corundum brick: Al2O3 content ≥90%.
It can be seen from the classification that silica bricks, clay bricks, and high alumina bricks are all commonly used refractory bricks for kilns. Often used for masonry kiln working layer, permanent layer, etc. Below we introduce the application of aluminum-silicon-based refractory bricks.
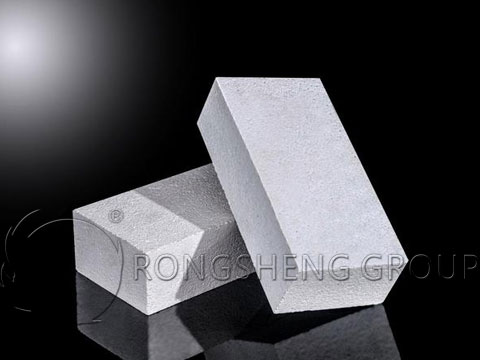
Alumina Silicate Refractory Bricks and Their Application Range
- Silica brick. Partition wall and lining of coke oven carbonization chamber and combustion chamber, the lining of hot blast stove roof and regenerator, small electric furnace roof masonry, glass kiln roof, acid steel furnace, and firing kiln dome.
- Semi-silica brick. Mainly used in coke ovens, acidified iron furnaces, metallurgical furnace flues, ladle linings, molten iron tanks, glass kilns, heating furnaces, hot blast stove tops, boiler combustion chambers, etc. Semi-silica bricks are not only used in these parts but can also be used as raw materials to make refractory materials with better quality, such as flow steel bricks.
- Clay bricks. Clay bricks are used to build heating and heat treatment furnaces, flues, open hearth regenerator checker bricks, and the bottom of regenerator walls. The lining of air ducts and gas ducts, dust collectors of iron furnaces, and linings of flues. The drying zone and preheating zone of the rotary kiln are lined. It is also a commonly used refractory material in furnaces such as boilers, lime kilns, glass kilns, and ceramic kilns.
- High alumina brick. Masonry blast furnace, hot blast stove, ladle, rotary kiln lining, and other metallurgical kilns. High-alumina bricks can also be used as lattice bricks on hot blast stoves to stack regenerators.
- Mullite bricks. Mullite bricks are commonly used in hot blast furnaces for ironmaking at high temperatures above 1200°C, parts of torpedo tankers impacted by molten iron, and slag lines. Furnace roof of steelmaking electric arc furnace, ceramic industrial furnace, regenerator arch, the superstructure of glass melting furnace, cement, rotary kiln lining, etc.
- Corundum brick. Used in blast furnaces, hot blast furnaces, and refining furnaces in the metallurgical industry. Second-stage furnaces, gasification furnaces, gas-making furnaces, cracking furnaces, and various high-temperature heating furnaces in ceramics, building materials, and other industries in the petrochemical industry.
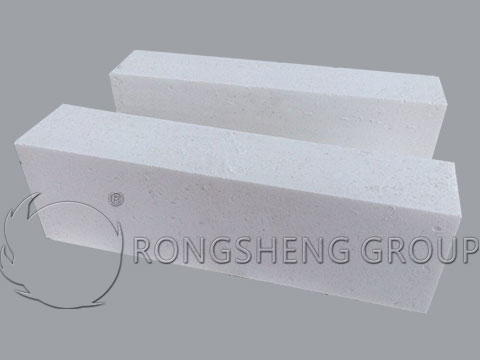
It can be seen from the above list that aluminum-silicon-based refractory bricks are widely used in various kilns. One kind of refractory brick can be used for the refractory lining of many kinds of thermal furnace equipment, and one kind of kiln needs many kinds of refractory bricks. Therefore, when users communicate with refractory manufacturers about aluminum-silicon-based refractory bricks, they should determine the location of use and the use environment, so as to choose the correct Alumina Silicate Refractory Bricks.
Good quality refractory bricks are the basic conditions for increasing the service life of the kiln lining. Choosing a strong refractory manufacturer not only saves procurement costs, but also ensures the quality of refractory materials, reduces the number of furnace shutdowns and repairs, and briefly increases production costs. Contact Rongsheng refractory manufacturers to get the most competitive price of Alumina Silicate Refractory Bricks.