Refractory plastic is made of 70~80% granular and powdery materials, 10~25% plastic clay and other binders, and appropriate plasticizers. Refractory plastic is a hard mud paste and is an amorphous refractory material that maintains high plasticity for a long time.
Refractory Plastic Materials
Refractory plastics are mainly used in various heating furnaces that do not directly contact the molten material. The materials are mostly clay and high-alumina, but also silicon, magnesium, chromium, zircon, and silicon carbide. If classified by binder, there are clay-bonded, water glass-bonded, phosphate-bonded, sulfate-bonded plastics, etc.
Aggregates for Refractory Plastics
Aggregates for refractory plastics mainly include special-grade clay clinker, third-grade, second-grade, or first-grade alumina clinker, etc. The maximum particle size of the refractory aggregate is 10mm, and its particle grading is: 10~5mm, 33%~40%; 5~3mm, 28%~35%, less than 3mm, 28%~35%. It should be pointed out that particles of 0.5~0.09mm should be minimized or eliminated. The amount of aggregate is 55%~65%.
Refractory powder is generally made of special-grade, first-grade or second-grade alumina clinker. The fineness of ≤0.09mm should account for 95%, and the finer the better. It is strictly forbidden to use underburned materials or clay clinker as refractory powder. The amount of refractory powder is 20%~30%.
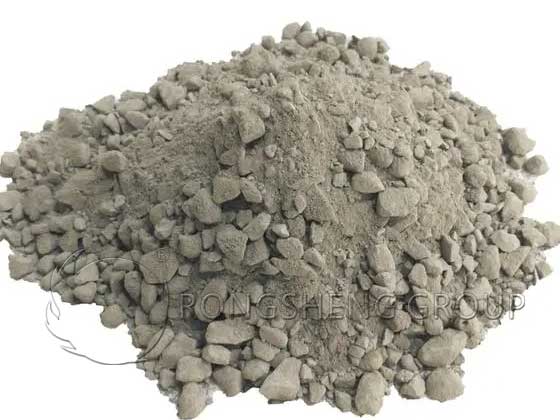
Performance of Refractory Plastics
In order to ensure smooth construction and normal use at high temperatures, refractory plastics should generally have the following basic properties: ① have a certain degree of plasticity to facilitate construction; ② have a certain shelf life to ensure that the molding performance remains unchanged during the specified storage period; ③ have a certain strength after room temperature curing to facilitate the removal of the frame or transportation after construction; ④ have a certain high temperature volume stability to prevent damage to the furnace lining structure due to excessive deformation.
Plasticity of Refractory Plastic
Since it is called refractory plastic, what does its plasticity have to do with?
The plasticity of plastic has a direct impact on the characteristics of clay and the amount of clay added. It is also related to the amount of water added. Plasticity increases with the increase of water added. But it cannot be too high, generally 5~10%. To improve plasticity, it is necessary to control the amount of clay and water added in the plastic, and plasticizers can be added.
The role of plasticizers in refractory plastics: ① Increase the hygroscopicity of clay particles, so that clay particles are dispersed and coated with water film; ② Make clay particles sol; ③ Increase the electrostatic repulsion between clay particles and stabilize the sol; ④ Exclude ions that hinder solification from the system as insoluble salts; ⑤ Increase the viscosity of water in clay to form a solid water film, etc. Commonly used plasticizers are pulp waste liquid, cyclohexane acid, lignin sulfonate, lignin phosphate, lignin chromate, etc. At the same time, the binder used in refractory plastics also has a certain influence on plasticity.
Soft clay is an important raw material for refractory plastics, and the main performance characteristics of plastics also come from soft clay. In refractory plastics, soft clay not only acts as a binder, but also as a plasticizer and sintering agent. It has a great influence on the plasticity, water retention, construction, room temperature, and high-temperature refractory properties of refractory plastics. Therefore, the soft clay used to prepare refractory plastics should have good plasticity, hygroscopicity, moderate viscosity, refractoriness and sintering properties. From the perspective of molding and water retention, the best viscoplasticity is Guangxi clay and ash clay, the worst is Fuzhou clay, Jiaozuo clay, camphor clay, and purple wood clay can be used in combination. Its fineness: less than 0.09mm accounts for more than 85%, and the dosage is 10%~15%.
The chemical binder is aluminum sulfate solution with a density of 1.2~1.3g/cm³. After mixing with this binder, the material should be trapped for more than 16h. Because the sulfate in aluminum sulfate reacts with the iron in the powder to generate iron sulfate and release hydrogen, which causes the mud to bubble or swell, the material should be trapped. After drying, there is a light yellow precipitate on the surface of the refractory plastic, which is identified as iron alum by chemical and petrographic analysis. Its molecular formula is FeO·Al₂O₃·4SO₃·22H₂O.
The 18 crystal waters contained in the aluminum sulfate solution are mostly removed at about 134°C. At about 330°C, a small amount of crystal water is lost. The endothermic peak at 835°C is the decomposition of aluminum sulfate into Al₂O₃ and SO₃, and SO₃ escapes in gaseous form. Therefore, the organizational structure of the refractory plastic is slightly loose and the strength is reduced. The endothermic peak in the low temperature section of the iron alum differential thermal curve is caused by the discharge of crystal water. The endothermic peak at 752°C is caused by the decomposition of iron alum and the release of SO₃. It also affects the strength of the plastic.
The amount of foaming of refractory plastic is directly related to the purity, density and addition amount of aluminum sulfate. Generally speaking, when the purity is high, the density is high and the addition amount is large, the amount of foaming is also large. This is due to the large amount of sulfuric acid brought in. Therefore, under the premise of meeting the plasticity, construction and fire resistance of the refractory plastic, crude aluminum sulfate can be selected to prepare a low-density solution and minimize its dosage. The dosage of aluminum sulfate solution is generally 9%~13%.
The additives used in refractory plastics mainly include preservatives, plasticizers, reinforcing agents and preservatives. Its additives include spodumene powder (LiO₂·Al₂O₃·4SiO₂), lithium mica powder (LiO₂·Al₂O₃·3SiO₂) and bentonite and other sintering agents (also known as mineralizers), and expansion agents such as kyanite or sillimanite.
There are many types of admixtures for refractory plastics, including polyvinyl alcohol, dextrin, starch, carboxymethyl cellulose, citric acid, gluconic acid and ethyl silicate. The dosage of admixtures is generally less than 1%, and when it is greater than 1%, it also acts as a binder. Other admixtures include andalusite, sillimanite, zircon and alumina powder, and their dosage is generally greater than 3%.
The maximum particle size of refractory aggregate is 10mm, the moisture content of plastic is about 9%, and the plasticity index is 17%~30%. Sunan mud refers to the composite use of Suzhou mud and Nanjing mud. The former has a high sintering temperature, while the latter has a low sintering temperature due to the high content of low melting points. Special clay and I alum, etc., represent special clay clinker and I alumina clinker, respectively. I and II alum are I and II alumina clinkers, which are mixed in a ratio of 1:1 to make refractory powder. Admixtures are selected according to the use requirements of refractory plastics. For example, if construction is carried out immediately after production, preservatives may not be added.
Rongsheng Refractory Material Factory is a powerful manufacturer and seller of refractory materials. Rongsheng Factory, an environmentally friendly, fully automatic monolithic refractory material production line, specializes in providing monolithic refractory products for high-temperature industrial furnaces, including various refractory castables, high-strength wear-resistant plastics, wear-resistant ramming materials, etc. Contact Rongsheng for free samples and quotation information.