What are aluminum carbon refractories? Special aluminum-carbon refractories refer to alumina and carbon as raw materials. In most cases, other raw materials such as SiC, metal Si, Al, etc. are also added. Carbon composite special refractory material bonded with organic binders such as asphalt or resin. Broadly speaking, refractories with alumina and carbon as the main components are called aluminum-carbon refractories. Aluminum-carbon refractories can be divided into two categories according to their different production processes. Non-burned aluminum carbonaceous refractories and fired aluminum carbonaceous refractories.
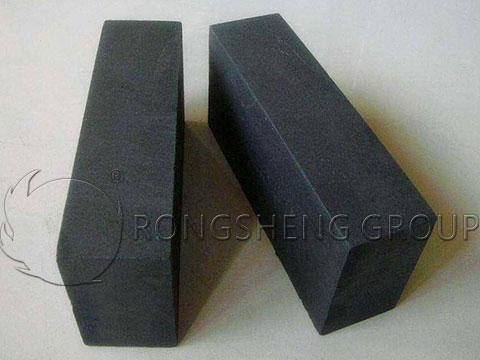
Introduction of Aluminum Carbon Refractories
Non-burning aluminum carbon refractories belong to carbon-bonded refractories. Because its oxidation resistance is obviously better than that of magnesia carbon bricks, and the corrosion resistance of Na2O series slag is excellent. Therefore, it is widely used in hot metal pretreatment equipment such as blast furnaces and hot metal ladle. The fired aluminum-carbon refractory is a ceramic-bonded refractory. Because of its high strength, corrosion resistance, and thermal shock resistance. Therefore, there are a large number of slide bricks suitable for continuous casting sliding nozzle systems and three continuous casting parts, namely, shroud, immersion nozzle, and integral stopper.
Alumina has high resistance to acid, alkaline slag, metal, and glass solutions. Whether it is used in an oxidizing atmosphere or a reducing atmosphere at a high temperature, it can be used well. The carbon raw materials, especially graphite, have high thermal conductivity and low linear expansion coefficient, and at the same time have non-wetting properties with slag and high-temperature solutions. Therefore, aluminum-carbon bricks have the following properties.
- (1) Aluminum-carbon refractories have excellent slag resistance and thermal shock resistance. Compared with magnesium-carbon refractories, aluminum-carbon refractories have better resistance to alkali corrosion and TiO2 slag erosion.
- (2) For fired aluminum-carbon bricks, silicon carbide is formed by the reaction of additive silicon and carbon at high temperature, so that it has a dual bonding system, namely carbon bonding and ceramic bonding. Therefore, the fired aluminum-carbon refractory has high mechanical properties. In continuous casting, it not only acts as a traditional refractory material but also a functional structural material.
At present, aluminum-carbon refractories mainly use fused corundum, sintered corundum, or sintered tabular corundum, super-grade or grade I high-quality bauxite clinker as the coarse-grained components of the products. Use corundum fine powder or fused mullite, sintered synthetic mullite fine powder, or synthetic high mullite fine powder. Adding a certain amount of carbon to the product is beneficial to improving the properties of the product and prolonging the service life. The melting point of carbon is very high, the coefficient of linear expansion is small, and the thermal conductivity is good.
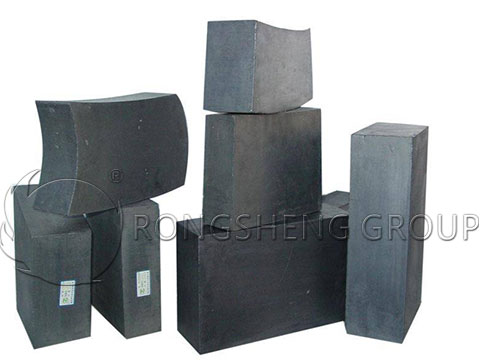
Carbon can penetrate into the pores of the particles in the product or form a vein-like network carbon chain structure between the particles to form a “carbon bond”, thereby reducing the porosity of the product and improving the high-temperature strength of the product. Carbon can also form a surface that is not corroded by metals and slag, improving the corrosion resistance and thermal shock resistance of products. In addition, the presence of carbon creates conditions for the reduction of iron and silicon oxides, and the resulting metal does not react chemically with refractory materials. When the oxide is reduced by carbon, the generated gas can prevent the molten oxide from penetrating into the refractory material. Carbon can also improve the thermal conductivity of the product, so as to prevent individual parts of the product from peeling and breaking due to uneven temperature overheating. Therefore, the carbon raw materials in the aluminum-carbon bricks are mainly flake-like natural graphite, and pyrolytic high-purity graphite can also be used, and carbon black is usually added. Antioxidants include metal Al, Si powder and SiC, B4C powder. Adding a small number of antioxidants can delay the oxidation of the carbon-containing layer and increase the service life of the product.
Purchase High-Quality Aluminum Carbon Refractory Materials from Manufacturers
To purchase high-quality aluminum-carbon refractories, please choose a strong refractory manufacturer. Rongsheng refractory material manufacturer has rich experience in the production and sales of refractory materials. Its customer base covers more than 60 countries all over the world. For example, Russia, South Africa, Kazakhstan, Philippines, Chile, Malaysia, Uzbekistan, Indonesia, Vietnam, Kuwait, Turkey, Zambia, Peru, Mexico, Qatar, etc. Moreover, a number of turnkey projects for refractory lining materials have been completed. Annual output of 80,000 tons of monolithic refractories. For more detailed information, please contact us.