In the preparation process of ultra-low cement refractory castables for the blast furnace tapping channel, the selection of refractory aggregates and refractory powders is very important. Only by selecting suitable refractory aggregates and powders, reasonably preparing them, and using them in proper amounts can they play their greatest role. Rongsheng refractory material manufacturer, an advanced fully automatic amorphous refractory castable factory, specializes in providing long-life refractory castable products for high-temperature industrial furnaces. Contact Rongsheng to get a free quote for ultra-low cement castables for tapping channels.
Selection and grading of refractory aggregates for ultra-low cement castables for iron trenches
In ultra-low cement refractory materials, the amount of refractory aggregate is generally 68% to 72%, which acts as a skeleton and can significantly affect the performance of the refractory castable lining. The thickness of the lining and the construction and production methods are different, and the critical particle size of the refractory aggregate is also different. At present, the critical particle size of refractory aggregates tends to decrease, and 8mm or 5mm is generally used. The preparation of iron ditch refractory castables usually adopts three-level gradation or four-level gradation. The particle gradation is as follows: 8~5mm 40%~60%, 5~1.2mm 10%~30%, 1.2~0.15mm 20%~40%. Or 5~3mm 40%~60%, 3~1mm 20%~30%, 1~0.15mm 15%~25%. Different types of refractory aggregates have different properties of the prepared ultra-low cement castables.
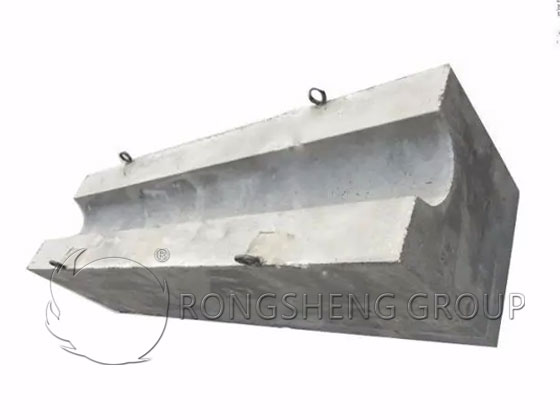
The influence of aggregate type and quality on the properties of castables. Different types of refractory aggregates have different drying compressive strengths of castables. That is, the quality of refractory aggregate directly affects its performance. Because good aggregate has low porosity and low water absorption, the castable requires less water and its performance can be improved.
Preparation of refractory powder for iron ditch castables
Refractory powder is the matrix material of amorphous refractory materials, which plays the role of filling aggregate gaps and improving construction and workability.
Refractory powder for iron ditch castables includes fused corundum powder, SiC powder, and carbon materials, among which the amount of fused corundum powder is 5% to 10%. The amount of ultrafine powder should be determined according to the experience of its variety, generally 5% to 15%. Among them, the appropriate amount of active SiO2 ultrafine powder is 5% to 7%, and the amount of other ultrafine powders is 7% to 10%.
Use of active SiO2 ultrafine powder and α-Al2O3 ultrafine powder
In ultra-low cement refractory castables, the basic mechanism of action of ultrafine powder is filling. In ultra-low cement refractory castables, various ultrafine powders can form colloidal particles in water. When a dispersant is present, the double electric layer formed on the surface of the particles overlaps to generate electrostatic repulsion, which prevents adsorption and flocculation between particles. At the same time, the dispersant is adsorbed around the particles to form a solvent layer, thereby increasing the fluidity of the castable.
The ultrafine powders used in Tiegou refractory castables mainly include active SiO2 powder and α-Al2O3 powder. The content of their components is 93.2% and >90%, respectively, and the particle size distribution <1.0μm should be >70%.
There are two types of SiO2 ultrafine powder. One is made of high-purity silica, and the other is a by-product of producing metallic silicon or ferrosilicon. The former is granular and inactive, while the latter is hollow spherical and active, does not agglomerate, and has good dispersibility and filling properties. It reacts with volcanic ash at room temperature and reacts with Al2O3 to form mullite at high temperature, which is beneficial to improving the strength of the castable.
α-Al2O3 ultrafine powder is made by calcining industrial alumina. Its characteristics are good dispersibility, small particles, easy sintering at high temperature and small volume effect.
Active SiO2 is added to ultra-low cement refractory castables. When the temperature is higher than 900°C, it reacts with Al2O3 in powder or cement. Mullitization is gradually formed, producing a volume effect, offsetting part of the volume shrinkage of the refractory castable, and promoting the improvement of strength. Adding α-Al2O3 ultrafine powder can cause calcium aluminate to form more calcium hexaaluminate (CA6) at high temperatures, as well as a small amount of mullite, anorthite, etc. The molar volumes of these minerals are relatively large, which prevents their volume from shrinking. Microscopic observation confirmed that the main crystal phase CA6 is a small columnar and needle-shaped crystal, and the anorthite is a small columnar crystal, which together form a small columnar and needle-shaped cross-skeleton structure, which is relatively strong and dense. Therefore, the strength of the castable can be significantly increased.
As the amount of ultrafine powder increases, the effect of cohesion and bonding increases, the strength increases, the volume density increases, and the apparent porosity decreases. However, increasing the dosage of SiO2 ultrafine powder will reduce the Al2O3 content in the castable. At the same time, the increase of free quartz will inevitably lead to a decrease in the slag resistance of the castable. Experiments have proven that when the dosage of SiO2 ultrafine powder is about 5%, the slag resistance is the best. In addition, adding more ultrafine powder will cause uneven shrinkage of the castable after high-temperature sintering, resulting in a significant decrease in strength.
Effect of ultrafine powder on the flexural strength of ultra-low cement castables. The ultrafine powder mixed with equal amounts of active SiO2 and α-Al2O3 has the highest strength. In fact, in ultra-low cement refractory castables, not only the fineness of the ultra-fine powder plays a role, but also its shape and activity. For example, SiO2 powder is silica fume, which is spherical and active, although slightly thicker. However, its filling and water-reducing properties are better than granular inactive α-Al2O3. Therefore, the dosage of active SiO2 ultrafine powder can also be less.
Effect of ultrafine powder dosage on the compressive strength of castables. As the amount of ultrafine powder increases, the compressive strength increases after sintering at 1600°C. When the dosage of SiO2 ultrafine powder is about 5%, the dosage of Al2O3 ultrafine powder is about 7%. At this time, the compressive strength is high and other properties are also excellent.
Use of silicon carbide and carbon materials
SiC and carbon materials should be added to the iron trench refractory castable to improve its slag resistance and thermal shock stability. Tests and use have shown that the grade and amount of SiC and carbon materials have a great influence on the performance of the castable. The grade and amount should be reasonably selected according to the size of the blast furnace and the different parts of use.
In the iron trench refractory castable, silicon carbide plays a filling role and forms the matrix of the iron trench material. Therefore, the particle size should be <3.4mm, of which <0.15mm should account for more than 60%. The particle size of the carbon material should also be less than 0.3mm.
Due to the addition of SiC and carbon materials, the oxidation resistance of the castable is reduced. To improve the oxidation resistance of the castable, metal aluminum powder and metal silicon powder can be added at the same time. In this way, metal silicon and aluminum react with carbon at high temperatures to generate SiC and Al4C3. The castable’s structure and surface are made denser, its oxidation resistance is improved, and the castable’s strength is also improved.