Lightweight thermal insulation refractory materials. The common characteristics of this type of material are low bulk density, light weight and low thermal conductivity. Rongsheng lightweight refractory insulation brick manufacturer, refractory insulation bricks, use temperature between 1000 ~ 1500 ℃, mainly lightweight clay bricks, lightweight silica bricks, lightweight high alumina bricks, etc. High temperature insulation bricks, use temperature above 1500 ℃, and can be directly used as the lining of high temperature kilns, mainly lightweight corundum bricks, alumina hollow ball products and zirconia hollow ball products. This article mainly introduces mullite insulation bricks. Contact Rongsheng for more information.
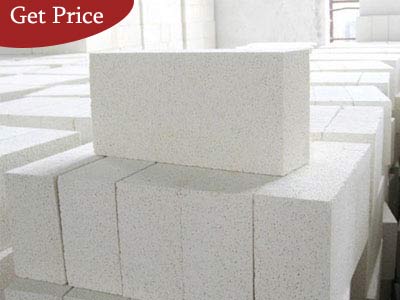
Mullite Insulation Brick
Lightweight mullite brick is a new type of energy-saving refractory material that can directly contact the flame and has the characteristics of high temperature resistance, high thermal shock stability, high strength, and low thermal conductivity. Mullite insulation bricks are widely used in the lining, furnace door bricks, kiln car bricks, etc. of ceramic roller kilns, shuttle kilns, cracking furnaces, hot air furnaces and various electric furnaces. The advantages are high purity, low impurity content, high temperature resistance, direct contact with flames, resistance to various atmosphere corrosion, low thermal conductivity, low heat melting, high strength, and excellent thermal shock resistance, high dimensional accuracy, and can be cut at will. The body density can be between 0.5 0.6 0.8 0.9 1.0 1.2 1.5 according to user requirements. It acts on high-temperature kilns and directly contacts the flame. It has good insulation effect, high compressive strength, and low thermal conductivity. It is suitable for electric kiln insulation, various high-temperature rotary kilns, tunnel kilns, nitriding gas kilns, etc. The crystals of fused mullite are larger than those of sintered mullite, and its thermal shock resistance is better than that of sintered products. Their high temperature performance mainly depends on the content of alumina and the uniformity of the distribution of mullite phase and glass. 1400 degree mullite bricks are mainly used for the top of hot blast furnace, blast furnace body and bottom, glass melting furnace regenerator, ceramic sintering kiln, dead corner lining of petroleum cracking system, etc.
JM23 lightweight mullite brick is a high-temperature resistant and energy-saving lightweight refractory material produced by Rongsheng Refractory Material Factory. Lightweight mullite brick has light weight and good thermal insulation effect. It is a high-quality high-purity refractory powder. According to the required specific gravity of the product, organic composite fillers are added, vacuum extruded and sintered at high temperature to form lightweight mullite products. Rongsheng manufacturers can customize different specifications of lightweight mullite bricks according to the actual working conditions of high-temperature industrial furnaces, and the content of alumina ranges from 50% to 80%.
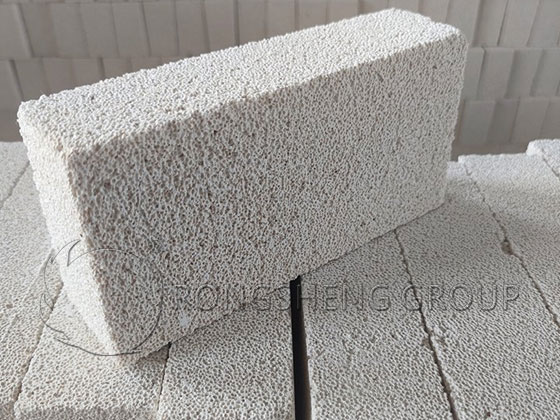
Characteristics of Mullite Lightweight Insulation Bricks
High temperature resistance can reach above 1790℃. The load softening start temperature is 1600-1700℃, and the compressive strength at room temperature is 70-260MPa. Good thermal shock resistance, high strength, low high-temperature creep rate, low expansion coefficient, small thermal coefficient, and resistance to acidic slag erosion. It can also greatly reduce the weight of the high-temperature furnace body, transform the structure, save materials, save energy, and improve production efficiency.
Lightweight mullite bricks are made of imported plate-shaped corundum and high-purity fused corundum as the main raw materials. They are made by mixing, drying, forming and firing in a high-temperature shuttle kiln using advanced ultrafine powder adding technology. Lightweight mullite bricks are widely used in equipment such as residual oil gasification furnaces, synthetic ammonia second-stage reforming furnaces, carbon black reactors and refractory kilns. The product’s dimensions, physical and chemical indicators and service life all meet customer requirements.
According to the chemical structure of lightweight mullite bricks, its outstanding performance is as follows:
- 1. Low heat melting. Due to low thermal conductivity, mullite series lightweight insulation bricks accumulate very little heat energy, and the energy saving effect is obvious in intermittent operation.
- 2. Low thermal conductivity, with good thermal insulation effect.
- 3. Low impurity content has very low content of oxides such as iron and alkali metals. Therefore, the refractoriness is high, and the high aluminum content enables it to maintain good performance under reducing atmosphere.
- 4. High hot compressive strength.
- 5. It can be processed into special shapes to reduce the number of bricks and masonry joints.
- 6. The appearance size is precise, which speeds up the masonry speed and reduces the use of refractory mud. The strength and stability of the masonry are guaranteed, thereby extending the life of the lining.
Application Scope of Mullite Insulation Bricks
Mainly used for high-temperature metallurgical hot blast furnaces above 1400℃, parts of torpedo cars impacted by molten iron, slag lines, furnace roofs of steelmaking arc furnaces, material channels of glass melting furnaces, regenerator arches, and upper structures. Ceramic sintering kilns, ceramic roller kilns, tunnel kilns, electric porcelain drawer kilns, and dead-angle furnace linings of petroleum cracking systems. Linings of glass crucible kilns and various electric furnaces, and the walls of clarifiers, which can directly contact the flame.