Refractory cement is a type of cement that is used in high-temperature applications. It is made from a combination of high-alumina cement, silica sand, and other materials that are resistant to extreme temperatures. Refractory cement is used in a variety of industries, including steel production, glass manufacturing, and ceramic production. Refractory cement is used to form a protective layer between the heat source and the equipment. It is designed to resist thermal shock, abrasion, and corrosion. Refractory cement is also used to fill cracks and gaps in the walls of furnaces and other equipment. It is also used to repair damage caused by thermal shock or abrasion.
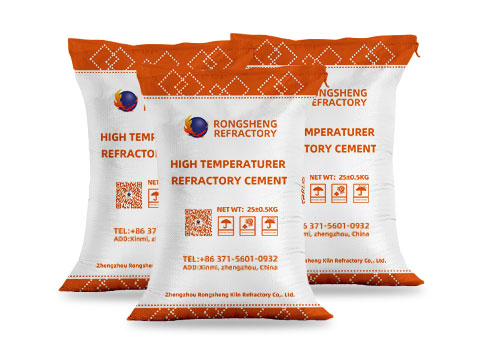
High alumina cement is the main component of refractory cement. It is made from a combination of alumina and calcium oxide and is highly resistant to extreme temperatures. This type of cement is also known for its high strength and durability. It is used in applications where temperatures can reach up to 3,000°F. Refractory cement is an important component of any high-temperature equipment. It is designed to withstand extreme temperatures and protect the equipment from damage. It is also used to repair damage caused by thermal shock or abrasion. Refractory cement is a reliable and durable material that can be used to ensure the safety and efficiency of any high-temperature equipment.
Castable refractory cement is a type of refractory cement that is used in applications where temperatures can reach up to 3,000°F. It is made from a combination of high-alumina cement, silica sand, and other materials that are resistant to extreme temperatures. This type of cement is used in applications where the cement needs to be poured or cast into a specific shape. Castable refractory cement is a type of cement that is used to line the walls of furnaces, kilns, and other high-temperature equipment. It is designed to withstand temperatures up to 3,000°F and is composed of high-alumina cement, which is a combination of alumina and calcium aluminate. Refractory cement is also known as castable refractory cement and cement refractory. And so is Cement refractory.
Refractory cement is an important material in many industries. It is used in applications where temperatures can reach up to 3,000°F, and is made from a combination of high-alumina cement, silica sand, and other materials that are resistant to extreme temperatures. It is used in steel production, glass manufacturing, and ceramic production.
Refractory cement can be used in a variety of ways. It can be used to make castable refractory cement, which is used to line furnaces, kilns, and other high-temperature equipment. It can also be used to make cement refractory, which is used to line fireplaces and other areas where heat is present.
Refractory cement is an important material in many industries. It is strong, heat-resistant, and can withstand high temperatures. It is used in a variety of applications, from steel and aluminum manufacturing to fireplaces and furnaces. It is made from a combination of high-alumina cement, silica sand, and other materials. Contact Rongsheng Refractory Manufacturers for free price information and samples.