The low cement series refractory castables are developed on the basis of clay-combined refractory castables. According to their content characteristics, they are mainly divided into low cement refractory castables, ultra-low cement refractory castables, and cement-free refractory castables.
The main characteristics of low cement series refractory castables are high volume density, low porosity, high compressive strength, good wear resistance, good thermal shock resistance and strong erosion resistance. In terms of construction, the advantages of low cement refractory castables are strong volume stability and low water consumption in construction. Because of these, low cement refractory castables are widely used.
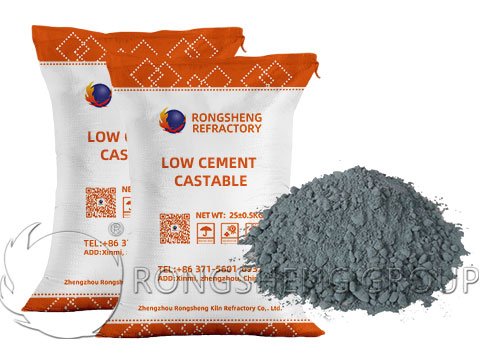
Classification of Low-Cement Series Refractory Castables
There is no national standard or industry standard for this product in the industry. Therefore, manufacturers have many names for this type of product, some are called dense high-strength refractory castables, some are called low-porosity refractory castables, and some are called low-moisture refractory castables based on the characteristic of low water addition during construction. In foreign countries, the United States classifies low-cement series products according to the calcium oxide content in the castable. Traditional cement castables (calcium oxide content greater than 2.5), low-cement castables (calcium oxide content between 1.0 and 2.5), ultra-low cement castables (calcium oxide content between 0.2 and 1.0), cement-free or ultra-fine powder castables (calcium oxide content less than 0.2).
According to the material of its main raw materials, it is divided into mullite low cement castable, corundum low cement castable, spinel low cement castable, aluminum silicate low cement castable, high aluminum low cement castable, etc.
According to its scope of use, it is divided into ladle refractory castable, iron ditch refractory castable, etc. Different parts of use can directly name the low cement refractory castable.
Compared with traditional aluminate cement castables, low cement refractory castables have a lower cement content. Generally, the cement content of low cement series products is less than 4%, and the water content is less than 11%.
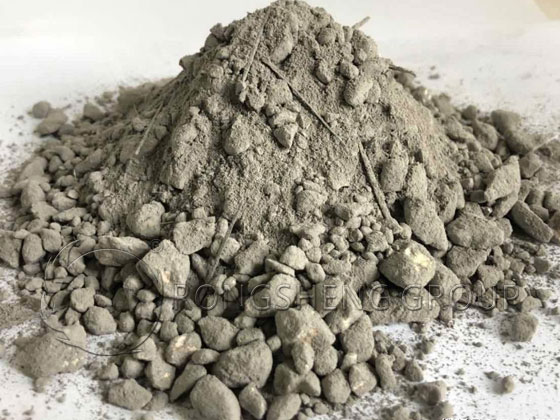
What are the Differences between Low-Cement Castables and Ordinary Refractory Castables?
Low-cement castables have the characteristics of high density, low porosity, high strength, low wear, thermal shock resistance and erosion resistance. They are mainly used in metallurgy, electric power, petroleum, chemical industry and various silicate kilns. Such as some components of off-furnace refining devices, off-furnace refining bag covers, electric furnace top linings, heating furnace soaking furnace linings, annealing furnace linings, tundish linings, steel tapping troughs, high-temperature burners and blast furnace iron tapping ditch covers, iron ladle linings, etc.
Low-cement castables have high fluidity. They are used as industrial furnace linings. On-site pouring, smearing and ramming construction methods can be used.
Low cement castables are similar to ordinary refractory castables. They are all composed of refractory aggregates, refractory fine powders and binders. The difference is that in the matrix composed of refractory fine powders and binders, fine powders are used to replace part or all of the alumina cement. A small amount of dispersant is added to evenly disperse the fine powders between the aggregate particles and fill them in the submicron-level gaps, thus forming a uniform and dense organizational structure. The key to this type of castable is the introduction of fine powders and their dispersion technology. In the field of amorphous refractory materials, ordinary cement castables have low medium-temperature strength and poor spalling resistance. The clay-bonded castables introduced in the early 1970s, although the medium-temperature strength has been improved, the room-temperature strength is much lower than that of ordinary cement castables. They cannot meet the needs of industrial furnaces and thermal equipment for refractory materials. In order to change this situation, low-cement high-strength refractory castables have been developed at home and abroad in recent years.
The main uses and advantages of low-cement castables. The use temperature of low cement castables and ultra-low cement castables is higher than that of ordinary refractory castables of the same material. The use temperature of low cement castables and ultra-low cement castables is higher than that of ordinary refractory castables of the same material.
Rongsheng Refractory Material Factory, environmentally friendly fully automatic monolithic refractory material production line, specializes in providing high-quality monolithic refractory material lining for high-temperature industrial furnace lining. Low cement castables, ultra-low or no cement castables, use micro powders with the same or similar chemical composition as the main material to replace most or all cement. Scientifically optimize factors such as particle grading, micro powder, particle morphology, etc., and add a small amount of dispersant (water reducer) and appropriate amount of retarder and other composite admixtures. Contact Rongsheng for free samples and quotes.
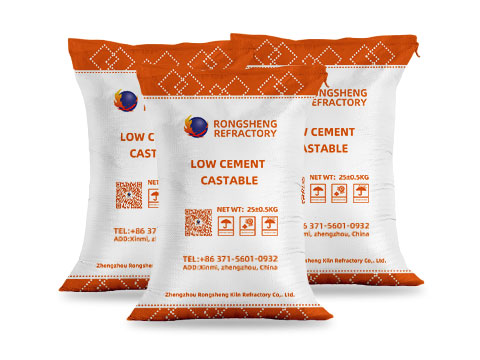
Physical and Chemical Properties of Ultra-Low Cement Castables
Ultra-low cement castables are a common category of refractory castables for cement kilns. Due to the continuous updating of technology in recent years, the problems of slow setting, hardening and low dry strength have been solved, and the problem of excessive strength after burning has been solved. Ultra-low cement refractory castables with excellent performance have been developed. The physical and chemical performance indicators of ultra-low cement castables made with the introduction of 0.5% CaO are as follows.
The flexural strength of ultra-low cement refractory castables after drying at 110°C is 9.8MPa and the compressive strength is 78MPa. After sintering at 1100°C, the flexural strength is 21MPa and the compressive strength is 155MPa. After sintering at 1500°C, the flexural strength is 18MPa, the compressive strength is 149MPa, and the line change after burning is 0.02%. These properties fully meet the requirements of cement companies. This ultra-low cement refractory castable is made of active calcium aluminate cement. If ordinary pure calcium aluminate cement is used with silica sol or diluted chain sol as an auxiliary binder, ultra-low cement refractory castables with similar properties can also be produced.