The aluminum melting furnace is an important piece of equipment in the aluminum processing industry, and the refractory lining, especially the non-stick aluminum castable used in the aluminum melting pool, plays a vital role in its normal operation at high temperatures. Liquid aluminum is lively and has a low viscosity. Therefore, the refractory materials in the molten pool that are in direct contact with molten aluminum are most severely damaged by molten aluminum erosion. Its quality and life will directly affect the quality of the product and the life of the aluminum melting furnace. So What’s the Best Proportion of Non-Stick Aluminum Castable for Aluminum Melting Pool?
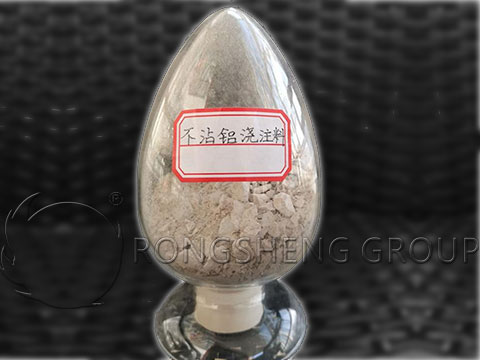
The Best Proportion of Non-Stick Aluminum Castable for Aluminum Melting Pool
Recently, it is time to repair the aluminum melting furnace and purchase refractory lining materials. Among them, in order to prepare non-stick aluminum castable for an aluminum melting pool with excellent resistance to aluminum melt corrosion. High alumina bauxite (8~5, 5~3, 3~1, and ≤1mm) is often used as aggregate, and fine mullite powder, α-AL2O3 powder, silica fume, barium sulfate, and high alumina cement are used as powder materials. After many times of running-in between refractory manufacturers and customers, The Best Proportion of Non-Stick Aluminum Castable for Aluminum Melting Pool. the best ratio of powder was finally obtained. The content of silica fume, anti-erosion agent, barium sulfate, and cement are 3%, 3%, 4%, and 4% respectively.
Analysis of the Influence of Fine Powder on the Corrosion Resistance of Castables for Molten Aluminum Pool
The erosion of the non-stick aluminum castable by the aluminum melt first occurs in the matrix. Therefore, in order to improve the corrosion resistance of non-stick aluminum castable for the aluminum melting furnace. In this experiment, in addition to using high alumina bauxite as aggregate, the influence of fine powder in the matrix composition on the corrosion resistance of the castable for the aluminum melting pool was also studied.
The raw material in the experiment is high alumina bauxite (8~5, 5~3, 3~1, and ≤1mm). The fine powder includes mullite fine powder (≤0.088mm), barium sulfate fine powder (≤0.045mm), α-AL2O3 fine powder (d=5μm), silica fume (≤1μm), high alumina cement, and anti-erosion agent. The basic ratio of the main raw materials is 71.71% high alumina bauxite, 5.29%-19.29% mullite fine powder, 5% α-AL2O3 powder, and the remaining matrix materials are silica fume, anti-erosion agent, barium sulfate, and cement. The anti-erosion performance of the materials after the ratio is analyzed as follows.
(1) With the addition of silica fume and the increase of its addition, the corrosion resistance of the sample gradually improves. This is because the particle size of silica fume is extremely small and can be filled in the voids formed by the coarse aggregate to densify the sample. As a result, the apparent porosity of the sample is reduced, and the passage of aluminum melt into the sample is reduced. In addition, the high proportion of silica fume has high reactivity, and it can promote the sintering of the sample matrix material at high temperatures so that the sample is densified and the strength of the sample is improved. The strength of the sample affects the ability of the castable to resist the stress caused by the metamorphic layer, and the stress change makes the corrosion caused by the appearance of cracks and cracks propagation intensified. It can be seen that the incorporation of silica fume can increase the strength of the non-stick aluminum castable while also improving the corrosion resistance of the sample.
(2) When the mixing amount of barium sulfate is 2%, the corrosion resistance of the sample can be increased from scratch to nearly double, and the corrosion resistance becomes excellent. It shows that the addition of barium sulfate can significantly improve the corrosion resistance of aluminum melt.
(3) With the increase of cement content, the corrosion resistance of aluminum melt of the sample has a tendency to decrease first and then increase. This is because the cement hydration increases the water requirement of the sample, and the dehydration of the hydration product at high temperature causes the internal structure of the sample to become loose, which weakens the structure and reduces the corrosion resistance of the sample. When the cement content continues to increase by more than 6%, the introduction of CaO into the matrix increases the amount of liquid phase at high temperatures. The surface tension of the liquid phase shortens the distance between the particles and promotes the internal densification of the sample. Thereby improving the aluminum melt corrosion resistance of the sample.
Summary: Non-stick aluminum castables are used for molten aluminum pools based on materials such as silica fume, corrosion inhibitor, barium sulfate and cement. The main factor that has an obvious influence on the corrosion performance of aluminum alloy melt is barium sulfate, and as the content increases, the corrosion resistance improves. Within a certain range, with the increase of the amount of silica fume incorporated, the corrosion resistance of the castable is improved. However, if the added amount of anti-corrosion agent and cement is controlled within a certain range, it can play a better anti-melt erosion effect.

Rongsheng High-Quality Unshaped Refractory Materials Manufacturer
Rongsheng is an experienced refractory material manufacturer and sales company. Rongsheng’s monolithic refractory production line has an annual output of 80,000 tons. Customers who purchase monolithic refractories from Rongsheng manufacturers each year have both new turnkey projects and furnace refractory lining repair projects. From the customer’s purchasing experience, they have not only experienced experiments with high-priced unsuitable refractory lining products, but also low-priced refractory lining materials that are not well used. Through various searches, the Rongsheng refractory manufacturer was finally selected. The product quality is qualified and the customer service is good. Formally because of this, Rongsheng continues to accumulate experience in the matching of customer projects and refractory materials, striving to provide customers with high-quality refractory products. Save production costs for customers and improve economic benefits. To choose high-quality refractory castables products, such as non-stick aluminum castables for aluminum melting furnaces, please contact us. We will provide you with unshaped refractory products that best suit your production needs according to your specific project needs.