The service life of refractory bricks used in the lining of the rotary kiln incinerator will affect the normal production of the rotary kiln. Of course, there are also rotary kiln-type incinerators that use refractory castables for integral pouring. So, is it better to use refractory bricks or castables for the lining of rotary kiln incinerators?
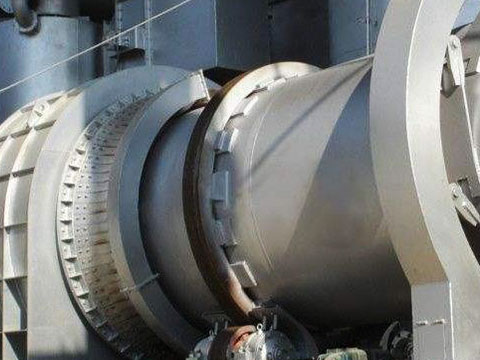
What are the Factors that Affect the Service Life of the Refractory Castable Lining of the Rotary Kiln Incinerator?
The thermal stress generated by the rapid cooling and rapid heating of the rotary kiln-type incinerator affects the service life of the inner lining. If the refractory castable for the lining is mainly alumina, add a certain proportion of silicon carbide to prevent acid corrosion. Refractory castables used in rotary kilns are also prone to falling off of tuyere materials. The performance of the castable itself and the on-site construction quality control is not in place, which easily causes abnormalities in the rotary kiln equipment. Coupled with frequent start and stop, it will aggravate the falling off of the lining of the rotary kiln.
To solve the problem of the castable burst. According to the requirements of different castables, the amount of water added should be less than more. The addition of an explosion-proof agent to the castable can make the refractory castable form a mesh-shaped micro-crack channel in the matrix when the refractory castable is heated and dry, which increases the air permeability of the refractory castable.
Different parts of the rotary kiln have different temperature requirements during normal operation and use, and it is necessary to select refractory lining materials according to the requirements of each part. A 50 mm thick thermal insulation refractory is built close to the outer layer, a 180 mm thick high-temperature refractory castable is poured in the high-temperature calcination part, and a 180 mm thick ordinary refractory concrete is poured in other parts. This effectively prevents the lining from falling off, reduces the number of maintenance, and prolongs the life of the rotary kiln.
Commonly, the refractory castable for rotary kiln-type incinerators is easy to fall off, the lining life is short, the operation rate is low, and the production cost is high. Of course, the proportion of refractory bricks used in the refractory lining of rotary kiln-type incinerators will be higher than that of refractory castables.
Advantages of the Refractory Brick Lining of Rotary Kiln Incinerator
The ratio of refractory bricks used in rotary waste incinerators is still higher than that of castables because of easy maintenance. Refractory bricks are sintered at a high temperature to perform better. But the material of bricks still needs to be cautious. Some users want to purchase silicon-molecular composite bricks for the refractory lining of incinerators. After analysis by refractory manufacturers, due to the bulk density of silicon-molecular composite bricks, in actual use, silicon-molecular composite bricks are not suitable for rotary waste incinerators.
So what kind of bricks are used in rotary waste incinerators? Refractory manufacturers recommend the use of anti-stripping high alumina bricks. With the addition of zirconia to the anti-stripping high alumina brick, it has high strength and resistance to acid and alkali corrosion, and its price is lower than that of silicon-mo composite bricks, and its service life is longer.
Regarding the selection of refractory lining materials for rotary kiln incinerators, whether it is to use refractory bricks or refractory castables, it is necessary to continuously summarize the experience in production practice. Strive for the best match between process and technical conditions, and finally achieve high-yield, high-quality, long-life, and low-cost efficient operation of the rotary kiln.