High alumina refractory bricks and fireclay refractory bricks are the two most commonly used refractory materials in shaped refractory materials. High alumina bricks have high refractoriness, good slag resistance, and high load softening temperature. The refractoriness of clay bricks is lower than that of high alumina bricks, and the slag resistance, especially the performance of acid slag resistance is better than that of high alumina bricks, and the thermal shock performance is good. Manufacturers of high alumina refractory bricks can provide methods of using high alumina refractory bricks to use high alumina refractory bricks more efficiently.
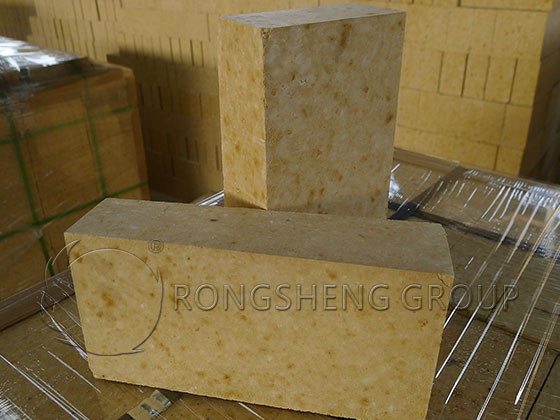
How to Use High Alumina Bricks
- The lining of important parts and parts with complex shapes should be pre-built first. For the lining with a complex structure and a large amount of refractory brick processing, it can be considered to change to the castable lining.
- The exposed metal parts left in the brick lining, including brick supporting boards, brick retaining boards, etc., should be sealed with special-shaped bricks, castables, or refractory fibers. It should not be directly exposed to hot kiln gas in use.
- Anchor bricks are masonry structural bricks, which should be set according to the design regulations and must not be omitted. Cracked anchor bricks shall not be used around the hanging holes. The metal hooks should be laid flat and hung firmly. The hanging hole and the hook cannot be stuck, and the gap left can be filled with refractory fiber.
- The expansion joints in the refractory brick lining must be reserved according to the design and must not be missed. The width of the expansion joint should not have a negative tolerance, and no hard debris should be left in the joint. And fill the seam with refractory fiber to avoid the phenomenon of being full on the outside and empty on the inside. Generally, expansion joints may not be provided in the heat insulation layer.
- When building capping bricks, joint bricks, and curve bricks, if the refractory bricks cannot meet the sealing requirements, the refractory bricks should be finished with a brick cutter, and the hand-processed refractory bricks should not be used. The size of the processed refractory bricks should not be less than 70% of the original refractory bricks. In the joint bricks and corner bricks of the plane, it shall not be less than 1/2 of the original brick. Must use the original brick lock.
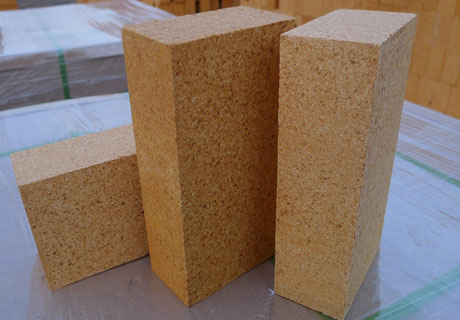
How to Use Fireclay Refractory Bricks
- The selection of the starting point should be laid sequentially from the hot end to the cold end or from the low end to the high end.
- Arranging and marking the operating points.
- Brick selection, according to the need to use the fireclay refractory bricks of different materials in the hot and cold sections, select qualified bricks.
- If there are anchor nails or supporting bricks, weld the anchoring nails or supporting bricks.
- If there is a heat insulation layer (such as silicon-calcium board, etc.), it is necessary to install the heat insulation layer first.
- For mortar preparation and application, the mortar mud should match the refractory bricks.
- Laying bricks.
- Reserve and fill the swelling gap.
How to ash the general refractory brick?
Ashing is to pre-apply mud on the bonding surface of the refractory bricks to be built. According to the change of the type, shape, and location of the refractory bricks, the method of ashing is also different. The unevenness of the dusting process has a great influence on the strength of the masonry. When the dusted refractory bricks are opened for inspection after the masonry is completed, it can be seen that the joints are evenly covered with mud. However, refractory bricks with poor ash removal will have gaps on the contact surface, which will reduce the cohesive force of the brick body and may cause air leakage in the masonry.
(1) Clay ash with a trowel. He holds a brick in his left hand and a tile knife in his right. When the plastering method is used to make gray strips, the mortar is first taken with a trowel, and then the bricks are taken. When laying the gray strips, place one large side of the brick upwards. When laying the bricks in place, press the bricks tightly with your left hand, and tap with a mallet in your right hand until the bricks are finally tightened.
(2) Shovel ash. Hold the refractory brick in your left hand and a large shovel in your right hand. First use a large shovel to beat the mortar, and then take the refractory bricks. These operations are the same as the trowel ash. Attention should be paid to the four movements in the picture. The tip of the shovel moves backward along the edge of the refractory brick so that the mortar will naturally form a raised back for masonry.
Regarding the use of high-alumina refractory bricks and clay refractory bricks, Rongsheng refractory material manufacturers have put forward the above suggestions, hoping to help you when choosing high-alumina refractory bricks and clay refractory bricks. The refractory brick products of Rongsheng refractory brick manufacturer include special grade high alumina brick, first-grade high alumina brick, second-grade high alumina brick, third-grade high alumina brick, clay refractory brick, clay insulation brick, high alumina insulation brick, corundum brick, Corundum mullite bricks, magnesia bricks, magnesia carbon bricks, magnesia chrome bricks, etc. Rongsheng refractory brick manufacturers can also customize refractory bricks according to the actual needs of industrial furnaces or construction drawings. Contact us for free prices and samples, Email: inquiry@global-refractory.com, Tel/WeChat/WhatsApp: +8618538312977.