Alumina Silicate refractory materials can be divided into the following three types according to the alumina content. Semi-silica (15%-30% alumina), clay (30%-48% alumina), and high alumina (alumina greater than 48%). In addition to making fired bricks or unfired bricks, it can also make molten cast products, as well as various grades of ramming materials, castables, refractory coatings, and other unshaped refractory materials.
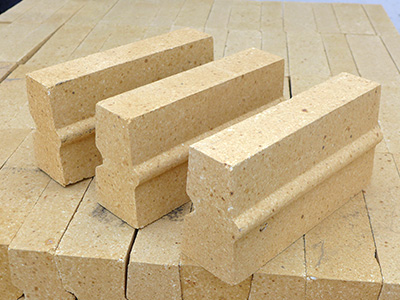
Advantages of Alumina Silicate Refractories
Alumina Silicate refractories have the advantages of a lightweight, high-temperature resistance, thermal stability, low thermal conductivity, small heat capacity, good mechanical vibration, good heating and heat preservation performance, and good expansion. Aluminum silicate fiberboard, aluminum silicate fiber felt, and aluminum silicate fiber blanket products made by special treatment. Model sealing materials have the characteristics of low thermal conductivity, high-temperature resistance, lightweight, long service life, high tensile strength, good elasticity, and non-toxicity. It is a new type of material to replace asbestos and is widely used in thermal insulation in metallurgy, electric power, machinery, chemical, and other industries.
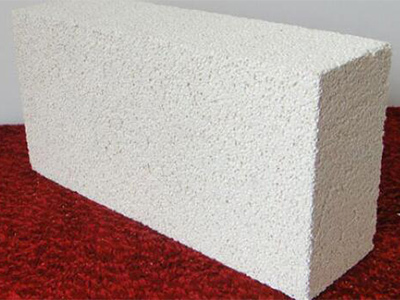
The Development of Alumina Silicate Refractories
Alumina Silicate refractory materials have a long history, and aluminum silicate refractory materials have been used in the bronze period about 1700 BC. Later, due to the rise of iron smelting and silicate industries, aluminum silicate refractories changed from natural raw materials to products such as saggers, crucibles, and blocks. After the nineteenth century, Alumina Silicate refractories became the main material for various furnace linings.
Since the 1960s, aluminosilicate refractories have developed into high-quality, high-purity, and indeterminate varieties. Since the founding of the People’s Republic of China, my country has manufactured many high-quality products of the world’s advanced level and has gained rich experience in the production of Alumina Silicate refractories. Refractory materials are mainly aluminum silicate, accounting for more than 85% of the total refractory materials, and high-aluminum and amorphous refractories are also increasing year by year. Since the 1980s, products in the steel industry have continued to emerge. Up to now, the lining of steel drums still uses aluminum silicate. The ladle used by Anshan Iron and Steel is lined with A120, which is more than 45%. Clay or high-alumina bricks are also used for steel. Many high-alumina bricks are used in the United States and Japan, which have been used more than 100 times. The life span of my country’s primary-fired high alumina bricks is 31-47 times. Clay bricks for coke ovens are of similar quality to similar products in Japan. Our homemade mullite slabs are better than non-fired high alumina bricks, such as corrosion resistance, no cracks, smoothness, and non-sticky slag. The mullite bricks used in torpedo bags developed by our country exceed the Japanese standards. Mullite plug bricks can be used in steel mills for more than four hours.
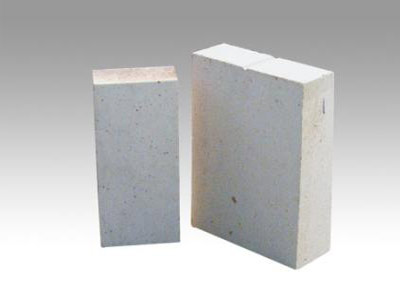
In the past 20 years, silicate aluminum refractories have moved towards high quality and high efficiency. Clay bricks are decreasing year by year, and high-alumina products are increasing year by year. Although the total amount of ordinary clay bricks has a downward trend, their role in industrial kilns and thermal equipment has not decreased. In the iron and steel industry, mullite or corundum bricks are widely used in the hearth, waist, and belly of the steel industry. Ordinary clay bricks or high-alumina bricks are generally still used on the main part of the blast furnace. The aluminum oxide of fireclay bricks used in Japanese blast furnaces has increased from 38% to more than 42%, the apparent porosity has been reduced from 20% to 10%, and the compressive strength has more than doubled. The high-density clay bricks or kaolin bricks used in the Soviet Union have a life span of more than 10 years. The walls of medium-sized blast furnaces in the United States are still using dense clay or high alumina bricks. Clay bricks and high alumina bricks are also used in blast furnaces in West Germany, France, the United States, and Italy.
Most hot blast stoves in various countries use alumina silicate firebrick materials. When the air temperature is lower than 900 ℃, ordinary clay bricks are generally used. When the wind temperature is 900-1100℃, high alumina bricks, mullite bricks, or sillimanite bricks are used for furnace lining and checker bricks. When the wind temperature is as high as 1100℃, high alumina bricks and mullite bricks are generally used as furnace lining and checker bricks. There are semi-silica, clay, high alumina bricks, and mullite bricks in American hot blast stoves.

The Development Trend of Alumina Silicate Refractories
In order to adapt to the development of modern technology, refractories are also facing a new development. This requires refractory materials to use raw materials with high chemical purity to make the products dense and resistant to sudden temperature changes. It can withstand the corrosion of molten metal in a vacuum and various atmospheres, and has high mechanical strength at high temperatures, and can resist creep and other properties.
The basis for the development of high-quality Alumina Silicate refractory materials is high-quality Alumina Silicate refractory raw materials. In recent years, foreign countries have kept improving the quality requirements of aluminum silicate refractories. A lot of research has been done in the aspects of beneficiation, purification, synthesis process, and calcination technology. The purity of raw materials is improved, the degree of sintering is improved, the composition structure is uniform, and the performance is stable, which provides a foundation for the development of high-quality, high-purity, and high-efficiency products. The research and development of new lightweight Alumina Silicate refractories and amorphous aluminum silicate refractories is a focus of future development of aluminum silicate refractories. In recent decades, the rapid development of monolithic aluminum silicate refractories and the expansion of their use range is a major breakthrough in the production of Alumina Silicate refractories. This material is characterized by a simplified production process, a simple firing process, energy-saving, easy construction, and can adapt to various complex furnace body structure requirements.

Rongsheng‘s new fully automatic monolithic refractory castable production line will provide high-quality monolithic refractory products for the lining of your kiln equipment. Provide better solutions for your furnace repair. For more detailed information, please contact us.