Introduction to the Ingredients of Acid-Resistant and Refractory Coating Materials
Acid-resistant and refractory coating materials are prepared from acidic or semi-acidic refractory powder (less than 0.088 mm), binders, and coating additives. Acidic and semi-acidic materials that can be used include pyrophyllite, silica, cast stone, andesite, burnt gemstone, etc. Their acid resistance is 92% to 96% for pyrophyllite, more than 97% for silica, 98% for cast stone, more than 94% for andesite, and 92% to 97% for charred gemstone. In addition, in order to prevent cracking during the drying of the coating after construction, heat-resistant glass short fibers or aluminum silicate refractory short fibers (3 to 7 mm) can also be added.
Binder for Acid-Resistant and Refractory Coatings
The binding agents of acid-resistant and refractory coatings include water glass, silica sol, acidic aluminum phosphate (aluminum dihydrogen phosphate), etc. Rongsheng Refractory Material Manufacturers can use high modulus water glass (modulus not less than 3) when using water glass as a binder, and can introduce organic resin to improve its bonding strength and crack resistance. The organic resin is preferably water-soluble or water-based latex resin. Optional organic resins include water-soluble sodium methyl siliconate, polyvinyl acetate emulsion, polyacrylate emulsion, water-based urea resin, etc. When using silica sol as a binding agent, a silica sol with a Si02 content of 30% to 45% should be used. A silane coupling agent or organic resin emulsion can be added when used. When acidic aluminum phosphate is used as a binding agent, it needs to be baked at high temperature to solidify. During the heating process, condensed phosphate is formed to form a film. A curing agent can also be added to solidify it into a film. The curing agents that can be used include metal oxides, hydroxides, borates, silicon cyanide, etc.
Uses of Acid-Resistant and Refractory Coatings
Acid-resistant and fire-resistant coatings are mainly used for smoke windows and flues where acidic gas media passes. and surface coatings for certain linings of reactors with acidic media.
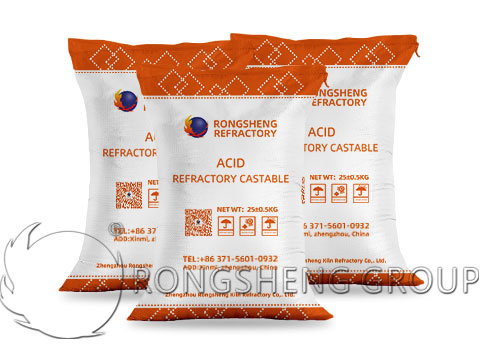
Special Performance Refractory Castable – Acid-Resistant Refractory Castable
Special performance refractory castables mainly include wear-resistant, acid-resistant, alkali-resistant, and high thermal conductivity castables. This type of castable is used in special kilns or locations, so it has special performance requirements.
Acid-resistant refractory castables are formulated with a water glass or cement as a binding agent and siliceous and aluminum silicate materials. Its characteristic is that it still has good performance under the action of medium and low temperatures and acid media. This type of refractory castable is used in blast furnace hot blast furnace dome protective layer, steel chimney lining and other equipment, and achieves good results.
The acid resistance of acid-resistant castables is affected by both physical and chemical factors. When the concentration of the acid solution is small, it will penetrate along the fine cracks of the product. The connection between aggregate and powder is destroyed and the strength is reduced. On the contrary, the acid solution has high viscosity and is difficult to penetrate, and at the same time, the chemical effect is strengthened. That is, the concentrated acid solution has an acidifying effect on the unreacted water glass and precipitates silicate gel to promote the strength growth of the castable.
At present, there is no standard to follow for the acid resistance of unshaped refractory materials. Under normal circumstances, according to the technical requirements of the project, the experimental plan is designed and the acid resistance test is carried out. Rongsheng refractory material manufacturers can customize refractory lining solutions according to the actual working conditions of the kiln lining. Contact us for free details.