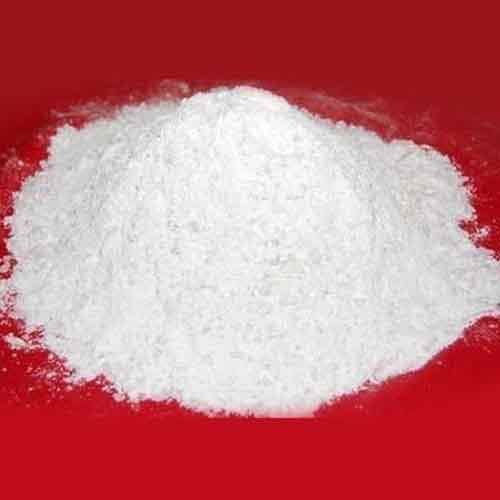
Induction Furnace Silica Ramming Mass
♦High refractoriness to with hold operating temperature
♦High corrosion resistance towards steel & slag
♦High electrical resistivity to prevent short circuiting
♦Suitable upto 1730ºC
♦Consistent quality (purity 98.65%)
♦Grain-sizes mixed according to capacity of the furnace
♦Free of iron oxide (FeO)
♦Minimum expansion & contraction at high temperature (treated)
♦Moisture free and sea worthily packing
♦Low down time for furnace lining
Silica Ramming Mass, also known as Acidic Ramming Mass, plays a crucial role in induction furnaces during melting of steel. This substance is used to line induction furnaces and its quality decides smooth working and more efficient output from the furnace. Ramming mass has a very important quality of withstanding of easily absorbing thermal shocks. It also does not develop cracks because of frequent power cuts during the operation of the induction furnace. Rong Sheng makes very high quality silica ramming mass containing very dense silica quartz.
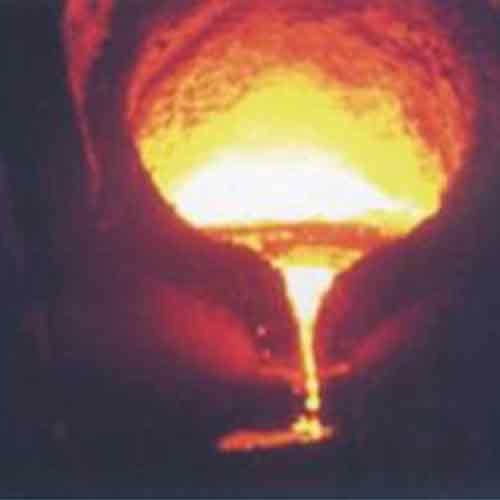
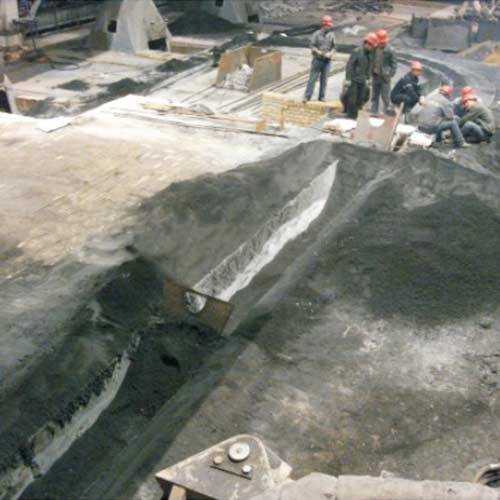
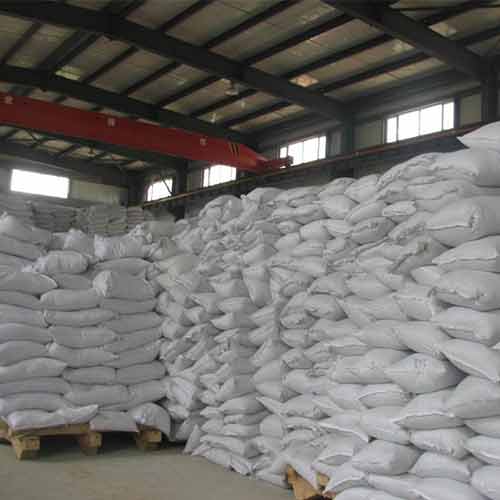
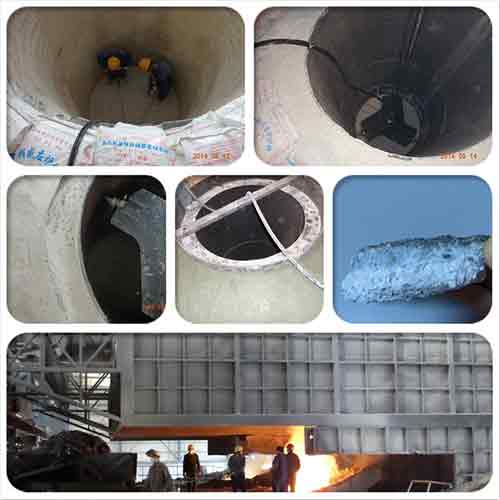
Applications of our silica ramming mass
Silica Ramming Rass (Acidic Ramming Mass) is used for the lining of smelting furnace etc thermal equipment such as ,Blast furnace iron runner and slag runner,Hot-blast cupola furnace,Lining of blast furnace,Molten steel ladle,Electric arc furnace(EAF),Matte smelting everberatory furnaces, Lining of inductionfurnace,Converter,Steel refining furnace,Rotary kiln etc.
Granularity Composition Of Silica Ramming Mass (%) :
4 mm to 1 mm 33 %
1 mm to 0.20 mm 30 %
0.20 mm to 0.06 mm 17 %
0.06 mm & Below 20 %
Specifications Of Silica Ramming Mass:
Silica | SiO2 | 98 to 99% |
Alumina | Al2O3 | 0.04% |
Titanium Dioxide | TiO2 | 0.08% |
Manganese Oxide | MnO | Nil |
Calcium Oxide | CaO | Nil |
Magnesium Oxide | MgO | 0.11% |
Sodium Oxide | Na2O | 0.05% |
Potassium Oxide | K2O | Nil |
Loss in ignition | – | 0.08% |
Sintering Temp. | 1200℃ | |
Max. Service Temp. | 1700℃ | |
Grain Sizes | 0 to 5 mm |