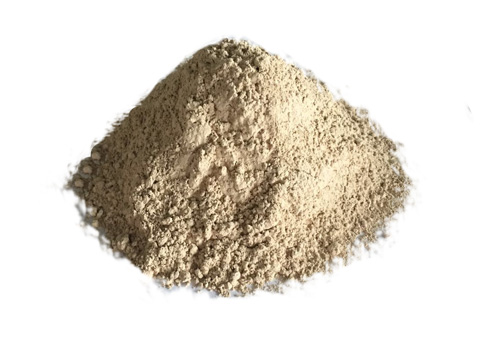
When it comes to a type of cement that can withstand higher temperatures that are common in foundries, smelters, ovens, bakeries, and other types of manufacturing processes high alumina cement is one of the best. It’s made by using bauxite, the aluminum ore, with lime. Normal cement is made by mixing silicate based minerals with lime instead. The two countries that use the most high alumina cement are the United States and the United Kingdom.
For Use In Foundries, Refractories, And Other High-Temperature Locations
In many manufacturing processes, there are high temperatures involved which can tend to break down standard Portland Cement. However, high alumina cement can withstand far higher temps than regular cement. It also tends to set up much faster and creates a lot of extra heat while doing so. This is a great advantage of high alumina cement since it can then be used in all types of northern climates during the winter months where other types of cement would never set up because of the cold weather.
It is also very resistant to many strong acids that are encountered in manufacturing lots of products from chemicals to foods and juices. Other types of cements can’t withstand the chemicals and deteriorate rapidly over time. High alumina cement is more costly, however, its longevity in many situations far outweighs the extra cost.
Another disadvantage of the alumina cement is in locations where it will be wet constantly and has failed in several high profile cases. As long as it’s not in a wet location it appears not to have any problems with failure. It has been used extensively in pre-cast beams that are used in many larger projects with great success.
If you’re looking at a certain project that could benefit from the use of high alumina cement there are specific guidelines that can help you determine if the added cost is worth it for you.