Refractory repair methods for blast furnace hearth-side walls. When high temperature occurs on the side wall of the blast furnace hearth, it needs to be solved by pressing in the side wall of the hearth. For high-temperature conditions on the side walls of the blast furnace hearth, it is first necessary to determine whether the cause is thinning of the lining or wind channeling from the back of the brick lining. Only when it is determined that there is back-channeling wind, it is necessary to press in. The pressed parts generally need to be determined by detecting the temperature changes of each part.
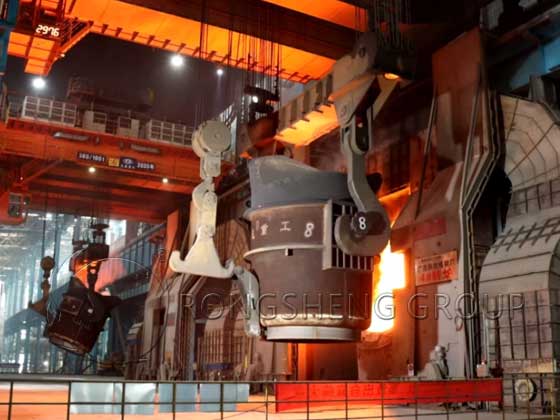
Refractory Repair of Blast Furnace Hearth-Side Wall
Generally, the pressed material is carbonaceous mud similar to the hearth brick lining material, or other non-hydraulic materials. For the press-fitting of the furnace side wall, there are three main forms depending on the structure of the furnace lining.
The first is the furnace lining structure using large carbon bricks. Because of this structure, there is usually a layer of carbonaceous ramming material between the large carbon bricks and the furnace shell or cooling stave. High temperatures in the hearth are often caused by gaps in the carbon ramming material layer, allowing high-temperature gas to pass through. Therefore, the key point of press-in grouting is to fill and seal these gaps with press-in material. At this time, the grouting position should be to use the reserved holes on the furnace shell or drill holes in the parts where the cooling wall can penetrate, and send the pressed material to the carbon ramming material layer.
The second is for the furnace lining structure using small carbon bricks. However, during design and construction, the carbon bricks are built close to the furnace shell or cooling stave. But in fact, due to various reasons such as manufacturing and installation accuracy, there is inevitably a gap between the carbon bricks and the furnace shell or cooling stave. At this time, the grouting method is the same as the first one.
The third type refers specifically to the furnace side wall having a cooling stave structure. When the surface temperatures of the furnace lining and the furnace shell rise simultaneously, it indicates that the gap between the cooling stave and the furnace shell has become a hot coal gas flow channel. At this time, it is necessary to grout the lining of the furnace while also grouting the space between the cooling stave and the furnace shell. The key to this grouting is to find the gas channel to determine the location of the drill hole. The depth of the drill hole must ensure that it penetrates the furnace shell without damaging the cooling wall. In this case, the pressed material can be selected from carbonaceous mud or other non-aqueous pressed materials based on actual conditions such as temperature and historical records.
For the press-in of the furnace side wall, the press-in point is generally determined by arrangement and blocking.
Repair of refractory lining materials, and design of refractory materials for high-temperature industrial furnace insulation layers. Rongsheng Refractory Materials Manufacturer is a refractory material manufacturer with rich experience in the production and sales of refractory materials. The quality of our refractory products is guaranteed and ready for shipment at any time. And our comprehensive customer service also protects the rights and interests of our customers.