How to choose refractory bricks when building flues? In addition to weight, the selection of refractory bricks for flues should also be based on the flue gas properties, temperature reduction, and whether it is corrosive. kiln fire bricks. Therefore, lightweight refractory bricks are generally used, such as lightweight mullite bricks, lightweight clay bricks, lightweight silica bricks, etc. They are light in weight and have excellent fire resistance and heat insulation.
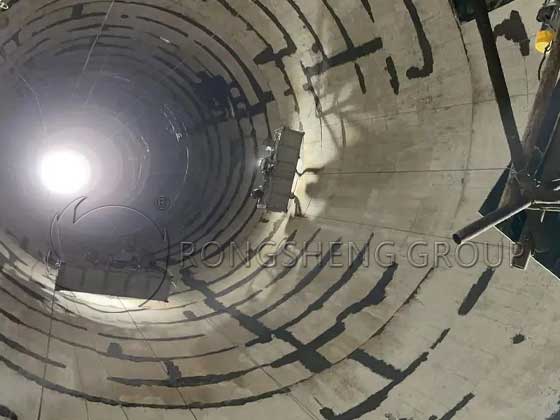
Refractory Bricks for Chimney Inner Wall
Refractory bricks are used for chimney inner wall. For round ones, special-shaped bricks, such as axe-shaped bricks or knife-shaped bricks, should be selected, and then some refractory casting materials should be added. For rectangular ones, standard refractory bricks are enough, and it is better to add casting materials.
The lining of chimney refractory bricks can be built with ordinary cement mortar, but it must be heat-resistant. Different industries may also have acid and alkali resistance requirements, and suitable refractory materials should be used.
How often should the acid-resistant bricks of chimneys be replaced? The quality and use conditions of acid-resistant bricks for chimneys produced by different materials and different manufacturers are different. Whether the chimney refractory bricks need to be replaced depends mainly on the degree of corrosion of the lining material of the chimney inner wall.
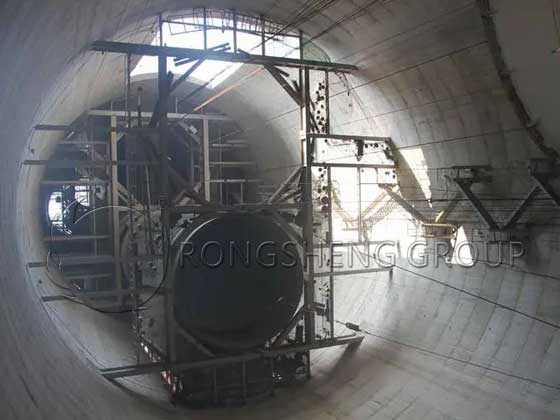
What are the Refractory Bricks Required for High-Temperature Flue Masonry?
Industrial chimneys are an important part of kilns. They are generally divided into red brick chimneys, concrete chimneys and steel chimneys, etc., and are lined with refractory bricks or refractory castables. kiln fire bricks. The size of industrial chimneys is determined according to the type of kiln and working conditions, and their shapes are mostly cylindrical.
The main function of industrial chimneys is to remove the waste flue gas in the kiln, and it also has the function of preventing the flame from burning in the furnace. When the temperature of the waste flue gas entering the chimney is high, its inner wall is generally built with a working layer. If the flue gas is acidic, acidic refractory bricks must be built, and lightweight refractory castables are also used. Rongsheng Refractory Material Manufacturer can provide high-quality high-temperature flue refractory bricks.
Since the temperature of flue gas is relatively high, the refractory bricks of flue should meet the characteristics of higher refractory bricks. However, some flue gas is corrosive when discharged, so refractory bricks need to be more corrosion-resistant. Therefore, when choosing refractory bricks for flue, in addition to considering the weight of flue, it is also necessary to choose according to the properties of flue gas produced by the medium. Such as the temperature of flue gas, whether it is corrosive, etc., so the refractory bricks of flue are generally based on lightweight refractory bricks. While reducing the weight of flue, it can also resist the scouring and corrosion of flue gas. Therefore, lightweight mullite bricks, lightweight clay bricks and lightweight silica bricks can be selected. In addition to light weight, these refractory bricks also have excellent fire resistance and thermal insulation. Ensure that the flue is not invaded by high-temperature heat flow, and at the same time, it can also resist the continuous scouring and corrosion of flue gas.
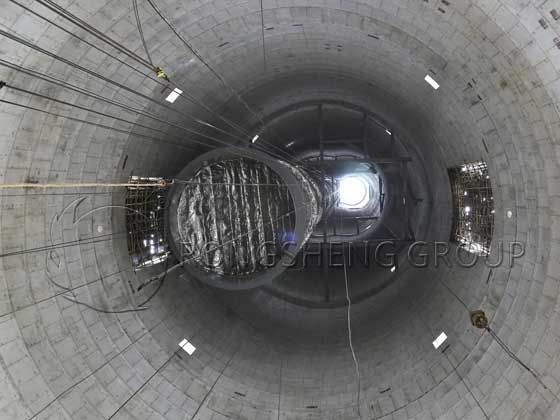
Refractory Bricks for High-Temperature Industrial Kilns
When choosing refractory bricks, you also need to make a reasonable choice based on the shape of the chimney, whether to use standard bricks or special-shaped bricks. If the chimney is round, you need to choose special-shaped refractory bricks, such as axe-shaped bricks or knife-shaped bricks. If the chimney is rectangular, standard refractory bricks can be used. kiln fire bricks. When laying bricks, you can choose to use high-temperature glue with the gap between bricks.
At present, the refractory bricks commonly used in chimney construction are: those that can absorb hydrogen fluoride should be alkaline refractory bricks, generally magnesia bricks. If the flue gas is acidic, refractory bricks resistant to acidic media should be selected. There are also common clay bricks, high-alumina bricks and silica bricks. When choosing, you should choose according to the properties of the flue gas.
The flue is the main device for high-temperature kiln exhaust gas emission, and it usually has to withstand the continuous scouring of high-temperature gas. Sometimes some flue gases are also corrosive, so when choosing flue refractory bricks, you usually have to choose bricks that are resistant to scouring and corrosion. At the same time, the bricks themselves also need to have a certain degree of fire resistance. Not only that, in order to reduce the pressure of the flue on the overall kiln and improve the stability of the flue, lightweight refractory bricks should be used as the main material.
Lightweight mullite insulation bricks
Currently, the refractory bricks that meet the above conditions mainly include lightweight mullite bricks, lightweight clay bricks and lightweight silica bricks. These bricks have good fire resistance, scouring resistance and corrosion resistance. Not only that, their weight is lighter than ordinary refractory bricks. Therefore, it is a good choice for building flues at present to ensure that the flue is not invaded by high-temperature heat flow, resist the continuous scouring and corrosion of flue gas, and reduce the overall weight of the chimney. When dealing with ordinary flue gas, we usually focus on lightweight mullite bricks and lightweight clay bricks. When facing gases with certain corrosive flue gas, we mainly focus on lightweight silica bricks because of its good corrosion resistance.
Lightweight clay bricks
When building flues, we need to choose according to the shape of the flue. Generally, for some round flues, special-shaped refractory bricks are mainly used, such as axe-shaped bricks or knife-shaped bricks. When facing some square flues, standard bricks can be used for masonry. When building, refractory mud is mainly used. Kiln fire bricks. It has a certain fire resistance and can ensure that the refractory bricks are closely connected. In the face of some occasions with corrosive flue gas, the refractory mud should also have a certain corrosion resistance.
Lightweight silica bricks
The above is the selection of flue refractory bricks. When choosing flue refractory bricks, in addition to considering the weight of the flue, you should also choose according to the properties of the flue gas produced by the medium. For example, the temperature of the flue gas, whether it is corrosive, etc., these are all things that need attention. kiln fire bricks. Choosing the right refractory bricks can not only improve the stability and thermal efficiency of the chimney, but also ensure the overall stability of the kiln. So pay special attention when choosing.