The main purpose of the carbon fiber graphitization treatment furnace is to induce the graphitization crystal orientation of the fiber to increase the elastic modulus of the carbon fiber. The production of carbon fiber is carried out in a high-temperature sealed graphitization furnace. Both ends of the furnace are sealed with high-purity argon gas. The heating element is made of graphite material, and the graphite tube is both the furnace tube and the heating element of the high-temperature furnace. The heating temperature is generally between 2500°C and 2800°C.
The life of the graphitization furnace depends on the properties of the refractory material. The furnace shell of the graphitization furnace is rolled from ordinary carbon steel plates. Special refractory materials are used as insulation materials in the shell, which are generally composed of heat-resistant layer, heat insulation layer and protective layer. In order to ensure the airtightness of the furnace, the inner surface of the refractory lining must be round and smooth. Otherwise, the air tightness of the lining will be affected and it will not be resistant to airflow erosion. In addition, there are temperature measuring holes and pressure measuring holes on the furnace.
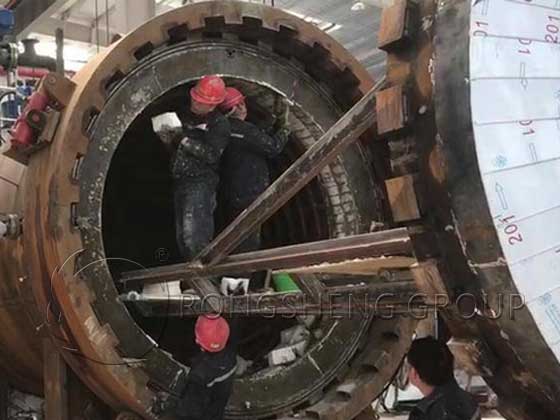
When using the graphitization furnace, great attention must be paid to temperature changes caused by rapid cooling and rapid heating. When production is stopped for maintenance, if the furnace cannot be kept warm by gas or other heat sources, the front and rear of the furnace must be tightly blocked to prevent the furnace from bursting due to rapid cooling. Prevent metal objects from entering the furnace and contacting the corundum lining, because metal and corundum materials generate a low melting point eutectic, which reduces the refractoriness and causes partial melting of the furnace body. The cooling water jacket must be designed reasonably to prevent burnout due to local overheating and to prevent water from entering the furnace and causing the furnace body to explode. In addition, carbon black fillers must not be affected by moisture. The graphitization furnace must be covered, and the flue gas must be treated to meet standards before it can be discharged.
Special insulation materials are selected as insulation materials for high-temperature graphitization furnaces, which refer to single materials such as high-purity oxides, non-oxides and carbon with melting points above 1800°C. Or they are made of various composite materials and produced using traditional production techniques or special production techniques. Its products are new refractory materials with special properties and special uses. The main function of high-temperature graphitization furnace insulation materials is to reduce heat energy loss and save energy. Ensure the needs of production process and improve equipment capabilities. Improve working conditions, achieve safe production, and extend the operation period of equipment.
Graphitization furnace insulation materials play the dual roles of heat preservation and electrical insulation in the graphitization furnace. Insulation materials have a very important influence on the temperature rise of graphitization furnace. The quality and thickness of the insulation material determine to a large extent the thermal energy utilization efficiency of the graphitization furnace and the temperature difference in various parts of the furnace, and determine the energy consumption during graphitization of carbon fiber. Insulation materials are also related to the safety and performance of refractory masonry and furnace building structures. The electrical insulation of the insulation material is key to ensuring that electric current acts effectively on the furnace tube. It requires low thermal conductivity and good thermal insulation performance. It has high resistivity and good electrical insulation properties. Does not hinder the discharge of gas in the furnace. Does not react with products in the furnace at high temperatures. Cheap and easy to purchase in large quantities.
Corundum (α-AL2O3) is produced by electrofusion or sintering of industrial alumina or bauxite ore. The mineral composition of corundum is a-AL2O3, its density is about 3. 85 ~ 4. 01g/cm3, its melting point is 2050°C, and its deformation temperature is 1750°C. It has good thermal conductivity, good electrical insulation and chemical stability, and can resist the erosion of NaOH, Na2CO3, etc. And it has the ability to resist the action of reducing agents (such as hydrocarbon chemicals, hydrogen and free metals, etc.) below 1800°C. It has the characteristics of high mechanical strength under high temperature, good thermal shock resistance, strong corrosion resistance, and small thermal expansion coefficient. It is the best lining material for various high temperature furnaces.
[Tips] Carbon fiber is a fibrous carbon material. Its biggest feature is its high elastic modulus and light weight. The deformation resistance of high elastic modulus carbon fiber is more than 2 times greater than that of steel and 5 to 6 times greater than that of aluminum alloy. The specific gravity of carbon fiber is less than 1/4 of steel and 1/2 of aluminum. Carbon fiber is a fiber with a carbon content of more than 90%, which is made from polyacrylonitrile fiber, pitch fiber, viscose fiber or phenolic fiber through oxidation, carbonization and other processes. Those with a carbon content higher than 99% are called graphite fibers.