G1, G2, G3, G4, G5, G6, G7, G8 clay bricks and high alumina bricks, these types of refractory brick masonry circles need to be carefully calculated. At the beginning of kiln design, calculating the brick type and quantity required for G-size bricks often makes people dizzy. Today, we will bring you specific calculation methods and construction points to help you design furnace types, calculate purchase quantities and provide references for construction.
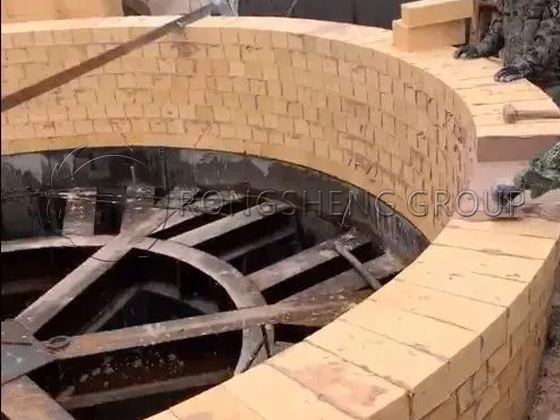
Calculation of the Amount of Furnace bottom Bricks
The volume of the bottom of the lime shaft kiln can be calculated by dividing the total volume of bricks by the volume of each brick. When calculating the number of bricks per layer, the horizontal cross-sectional area of the furnace bottom bricks can be divided by the corresponding surface area of each brick. Generally, a loss of 2% to 5% should also be considered. If the weight of the bricks needs to be calculated, the weight of each brick is multiplied by the number of bricks.
Calculation of the Amount of Ring Furnace Body
The other parts of the lime kiln are all ring cylinders or cones. Regardless of the upper and lower layers or the inner and outer layers, rings must be built, and wedge bricks must be used when building rings. If a ring of any diameter is built, wedge bricks and straight bricks must be used together. Generally, G-1 straight bricks are matched with G-3 or G-5 wedge bricks, and G-2 straight bricks are matched with G-4 or G-6 wedge bricks. Due to the different required ring diameters, the number of straight bricks and wedge bricks is also different.
If G-3, G-4, G-5, G-6 wedge bricks are used alone to build rings, the formula can be listed:
nx=(2πa)/(b-b1)
Where:
nx——Number of wedge bricks for building a ring, pieces;
a——Brick length, mm;
b——Width of the big end of the wedge brick, mm;
b1——Width of the small end of the wedge brick, mm.
From the above formula, we can know that the number n of wedge-shaped bricks used in each ring is only related to the width of the two ends of the wedge-shaped bricks and the length of the bricks, but has nothing to do with the diameter of the ring.
It can be concluded that:
Number of bricks needed to build a ring with G-3 is n=97
Number of bricks needed to build a ring with G-4 is n=87
Number of bricks needed to build a ring with G-5 is n=48
Number of bricks needed to build a ring with G-6 is n=54
At the same time, the inner diameters of the rings built with the above four wedge-shaped bricks are 4150mm, 3450mm, 1840mm, and 1897mm, respectively.
If you want to build a ring of any diameter, you need to use straight bricks and wedge bricks together. The number of straight bricks can be calculated by the following formula:
nz=(πd-nx*b1)/b
Where:
nz——Number of straight bricks, pieces;
nx——Number of wedge bricks, which is a constant after the brick type is determined;
b1——Width of the small end of the wedge brick, mm;
b——Width of the straight brick, mm;
d——Inner diameter of the ring, mm.
Example: Try to use G-3 and G-1 bricks to build a ring with an inner diameter of 7.2 m. Find the number of wedge bricks and straight bricks required.
Solution:
nx=97 pieces
nz=(πd-nx*b1)/b=3.14*(7200-97*135)/150=65 pieces
Construction points of G-type bricks
When building a lime kiln, two types of bricks can be used to build rings of different diameters to adapt to the size of the furnace and the change of furnace diameter with height. Generally, refractory bricks G1 are matched with G3 or G5 wedge-shaped bricks, and refractory bricks G2 are matched with G4 or G6 wedge-shaped bricks. Due to the different ring diameters during the masonry process, the number of straight bricks and wedge-shaped bricks is also different.
When the inner lining of the lime kiln is built, the ring seams are required to be built with all staggered seams, and bricks must not be cut. If bricks must be cut, the cut surface must be smoothed. The thickness and staggered seams of the masonry are combined with different brick types with brick lengths of 230 mm and 345 mm. The thickness of the masonry can be increased or decreased by 115 mm and staggered seams can be achieved by matching. When the thickness change is less than 115 mm, the filler seams between the masonry and the furnace shell or the masonry and the cold wall can be used to adjust.
Of course, the specific dosage calculation and construction methods of the above methods are not fixed. It depends on the on-site furnace conditions and usage requirements.